Ceramic Injection Molding (CIM) is an emerging technology for manufacturing complex-shaped ceramic parts, and it has incomparable unique advantages in the preparation of complex small parts. With the continuous expansion of the industrialization scale of electronic ceramics worldwide in recent years, the attractive application prospect of CIM technology is worth looking forward to. The process mainly includes material preparation, injection molding, debinding, and sintering.
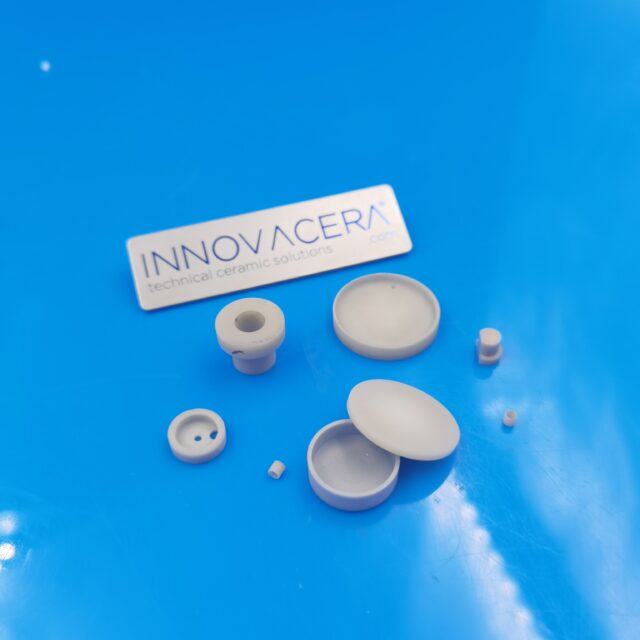
Injection Molding of Aluminum Nitride Ceramics
① Material preparation. The sinterable ceramic powder is mixed with a suitable organic carrier (binder) at a certain temperature to provide the fluidity and green strength necessary for ceramic injection molding; the mixture system of ceramic injection molding is a high-solid Viscous suspension (or melt) with phase volume fraction, the volume fraction of solid particles (ceramic powder) reaches 50-70%.
② Ceramic Injection molding. After kneading, the extruded and granulated mixed material is heated and softened at a certain temperature by an injection molding machine, and then injected into the mold at high speed under pressure, cooled, and re-solidified in the mold to obtain the desired shape of the injection molded blank. Mold shape, mold temperature, feeding temperature, injection pressure, holding time, cooling speed, etc. all have an impact on the quality of the billet.
③ Debinding. The organic binder for injection molding is about 25-50% (volume percentage). How to effectively remove such a large amount of organic matter without affecting the distribution of particles is a very difficult thing. Degreasing is a physical and chemical reaction process, and its process control is complex, which may easily cause defects such as cracking, deformation, and voids in the green body. Therefore, whether the degreasing can be successfully completed is very important for ensuring the quality of the green body, high product qualification rate, reducing energy consumption, and large-scale production.
④ Sintering. After degreasing, ceramic injection molded products will have many pores inside and low density, so high-temperature sintering is required to obtain high-performance dense products. The sintering speed is related to viscous flow, condensation, volume diffusion, surface diffusion, etc. For non-oxides, nitrogen or other gases are generally used instead of air, and the sintering of oxide ceramics is generally carried out under air. Sintering is generally carried out at normal pressure, but for some ceramics that are easy to evaporate at high temperatures, it must be carried out under pressure.
Advantages: high density, uniform density distribution, can be used for complex shape green body molding, and high molding precision, no need for post-processing.
Disadvantages: Defects such as underfill, flash, weld marks, and air pockets are prone to affect the sintering of AlN ceramics.