Due to the properties of ceramics, ceramic PCBs can be placed in high-pressure or high-temperature environments, traditional PCB substrate materials may exhibit flaws in extreme conditions. In the article, we will discuss three common ceramic PCBs.
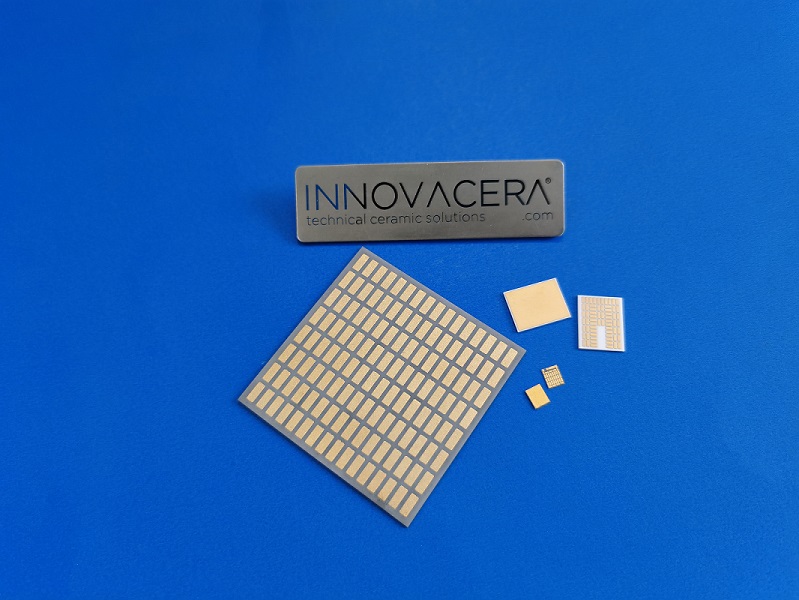
Metallized Ceramic PCB
The three most commonly used ceramic materials for PCB manufacturing are:
Alumina (Al2O3) – The mechanical strength, chemical stability, thermal conductivity, and electrical properties of Al2O3 is advantageous compared to other oxide ceramics. The abundance of a raw material makes alumina the most commonly used ceramic substrate material. Al2O3 ceramic PCBs are used in automobile sensor circuits, shock absorbers, and engines. The high thermal stability of Al2O3 ceramic PCBs improves the performance and thermal efficiency of the circuits used in automobiles.
Aluminum Nitride (AlN) – The high thermal conductivity and coefficient of expansion are two properties that make AlN noteworthy as a substrate material in the PCB industry. The thermal conductivity of AlN varies in the range of 170 W/mK to 220W/mK. The CTE of AlN ceramic matches with silicon semiconductor chips, which establishes a good bonding between the two, thus making their assembly reliable. AIN is used in sensor circuits in automobiles, as it can withstand extreme temperatures, corrosion, and vibration while providing efficient, accurate, and sensitive sensor signals.
Beryllium Oxide (BeO) – BeO is a ceramic PCB substrate material with a thermal conductivity around nine times that of Al2O3 and greater than metal aluminum. BeO showcases better chemical stability than AlN and high electrical isolation comparable with Al2O3e. BeO is used in applications where the PCB is subjected to high temperatures or in high-density PCBs facing space limitations to provide air or liquid cooling.